Cual es la funcion del eje del motor baldor m3353
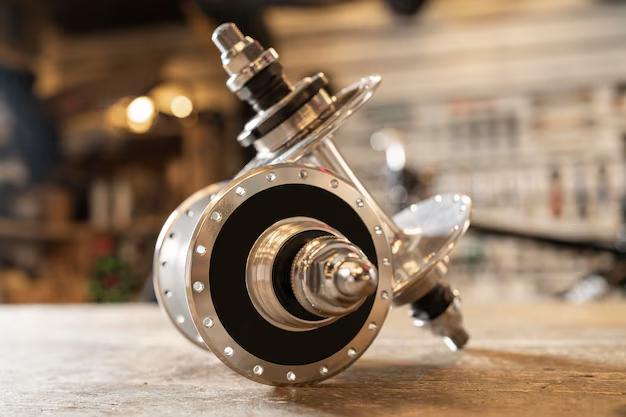
The function of the motor shaft, particularly in a Baldor M3353 motor, is integral to the operation of the motor in various industrial and commercial applications. Motors like the Baldor M3353 are widely used across industries, and understanding the role of the motor shaft can provide insights into the overall functioning and efficiency of the motor. In this article, we will dive into the purpose, construction, operation, and the impact of the motor shaft on performance, with a particular focus on the Baldor M3353 motor.
Introduction to Baldor M3353 Motor
Baldor Electric Company is known for its high-quality electric motors, offering a variety of motor types for different industries. The Baldor M3353 is an example of an industrial motor used for heavy-duty applications. Typically, this motor is an AC induction motor, designed for high torque and efficiency. It is often used in manufacturing, conveyor systems, and various other automation systems.
The motor shaft, a central part of the motor, is the component that converts the rotational energy generated by the motor into mechanical work. It serves as the interface between the internal workings of the motor and the external load that the motor drives.
Function of the Motor Shaft in the Baldor M3353 Motor
1. Transmitting Mechanical Energy
At its core, the motor shaft in the Baldor M3353 is responsible for transmitting mechanical energy. The motor converts electrical energy into mechanical energy via the rotation of the rotor inside the motor. This rotation occurs due to the electromagnetic forces acting between the rotor and stator.
The motor shaft is directly connected to the rotor, and it is this shaft that carries the rotational force generated by the rotor to external machinery. Whether the motor is driving a conveyor belt, fan, pump, or other equipment, the shaft ensures that the rotational motion is transferred effectively to these systems.
2. Connecting the Motor to External Equipment
The motor shaft serves as the physical connection between the motor and the external equipment that needs to be powered. It is commonly coupled with external components such as pulleys, gears, or couplings. These external elements often serve to adjust the speed, torque, or direction of the motion produced by the motor.
In industrial applications, precise coupling between the motor shaft and the driven load is essential to maintain the efficiency and safety of the system. Misalignment, wear, or improper coupling can cause mechanical failures or inefficiencies in energy transmission.
3. Support for the Rotor and Bearings
The motor shaft in the Baldor M3353 also provides support for the rotor and ensures that it spins within the motor housing. Bearings are typically used to reduce friction between the rotating shaft and the stationary components. The smooth rotation of the shaft reduces wear and tear, prolonging the motor’s lifespan and ensuring reliable operation.
The shaft is often supported at both ends by bearings, which allow it to rotate smoothly and with minimal resistance. Without these bearings, the friction caused by the rotation could generate excessive heat and potentially damage both the shaft and the motor components.
4. Maintaining Alignment and Stability
The shaft in the Baldor M3353 motor plays a critical role in maintaining the motor’s alignment and stability. For a motor to operate efficiently, the shaft must remain aligned along the motor’s axis of rotation. Any misalignment of the shaft could lead to vibration, noise, and potential damage to the motor.
The shaft is carefully designed to ensure that it maintains stability under heavy loads and high rotational speeds. This is especially important in industrial settings where the motor may be subjected to demanding conditions and must operate continuously for long periods.
5. Facilitating Speed and Torque Adjustments
The motor shaft allows for adjustments to the speed and torque output. In some cases, external gearboxes or pulleys are attached to the shaft, which allows for changes in the output speed and torque. The motor may be designed to operate at a certain speed or with a specific torque output, and adjustments to the shaft and coupling system allow it to meet the specific needs of the application.
In certain applications, the motor shaft might need to operate at different speeds to match the load. This capability is essential for systems that require dynamic adjustments, such as conveyors with varying load weights or pumps that operate at different flow rates.
6. Enhancing Motor Efficiency
The efficiency of a motor is determined by its ability to convert electrical energy into mechanical energy with minimal losses. The motor shaft contributes to this efficiency by ensuring smooth and direct transmission of rotational energy. A well-designed motor shaft reduces friction and energy losses, enabling the motor to operate at higher efficiency.
Additionally, the shaft design can affect the overall performance of the motor in terms of vibration reduction, which contributes to smooth and quiet operation. Vibration and noise not only impact user comfort but also lead to potential energy losses and mechanical wear over time.
Construction and Materials of the Motor Shaft
The construction of the motor shaft in the Baldor M3353 motor is carefully engineered to meet the specific requirements of the motor’s applications. Motor shafts are typically made from high-quality steel, stainless steel, or other durable alloys that can withstand the mechanical stresses generated during operation. These materials are chosen for their strength, hardness, and resistance to wear and corrosion.
In addition to the materials used, the shaft is typically treated with processes such as heat treatment, which enhances its hardness and resistance to wear. The shaft’s surface may also be finished with coatings to reduce friction and improve the overall durability of the component.
Types of Motor Shafts
Motor shafts come in various designs depending on the application and the motor’s design. The two most common types of motor shafts are:
- Solid Shafts: These shafts are made from a single piece of material and are typically used in applications that do not require high torque transmission. They are relatively simple in design and are used in applications where the load is not very heavy.
- Hollow Shafts: These shafts are used in applications that require high torque. Hollow shafts are generally stronger and lighter than solid shafts, and they allow for a reduction in weight while maintaining high strength. They also allow for easier integration of components like couplings and pulleys.
The Baldor M3353 motor is designed with a shaft that ensures optimal transmission of power and durability under various industrial conditions.
Maintenance and Longevity of the Motor Shaft
Regular maintenance is essential to ensure the longevity and efficiency of the motor shaft. The motor shaft and associated components like bearings need to be inspected periodically to check for signs of wear, misalignment, or damage. Common issues that may arise with motor shafts include:
- Wear and Tear: Over time, friction between the rotating shaft and bearings can cause wear, leading to a decrease in efficiency and performance.
- Misalignment: Misalignment of the shaft can cause vibrations, increased wear, and potential damage to both the motor and the equipment it drives.
- Corrosion: Exposure to moisture, chemicals, or extreme conditions can lead to corrosion of the shaft, affecting its performance and lifespan.
Preventative maintenance can include lubrication of the bearings, realignment of the motor shaft, and regular cleaning to remove dirt and debris that may cause friction.
Conclusion
The motor shaft in a Baldor M3353 motor plays an essential role in converting electrical energy into mechanical work, transmitting the rotational energy generated by the motor to external machinery, and ensuring the motor operates smoothly and efficiently. The design and materials used in the motor shaft contribute to the motor’s overall performance, longevity, and ability to withstand the stresses of heavy-duty applications.